Acetal (Delrin®) is a high-performance engineering thermoplastic widely used in the manufacture of high-precision mechanical parts such as gears and bearings. Not only does it have excellent mechanical properties, but it also has excellent dimensional stability.
The Machining of Delrin® often involves complex CNC machining techniques, which makes it irreplaceable in a variety of industries such as consumer electronics, automotive, and industrial equipment.
Acetal Advantages
- Mechanical Excellence
Acetal has excellent mechanical properties, including high impact resistance and low friction characteristics. - Dimensional Stability
Acetal demonstrates superior dimensional stability during CNC machining and is suitable for high precision products. - Temperature Resistance
Acetal is able to maintain performance over a temperature range of -40°C to 120°C for a wide range of environmental conditions. - High Processing Efficiency
Acetal is easy to cut and machine, reducing machine wear and shortening production cycles.
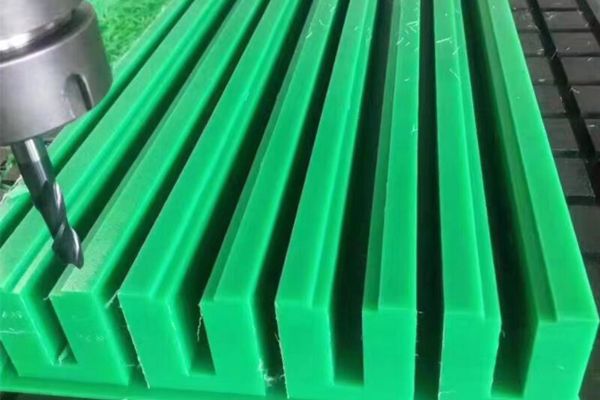
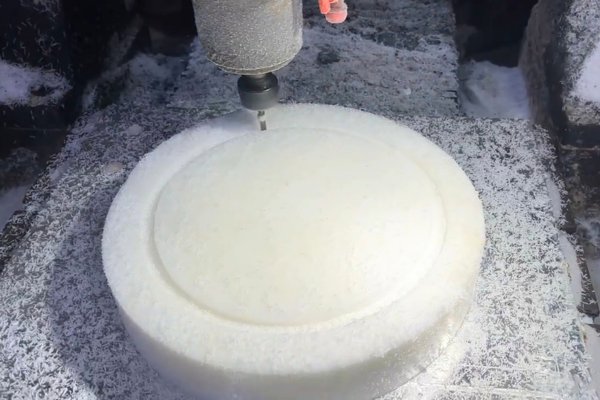
Acetal Machining Technology
- CNC Machining
Includes CNC turning, CNC milling and drilling. - Injection Molding
Suitable for mass production, such as quick couplings and fasteners. - Extrusion
For the production of Acetal rods, tubes and profiles. - Laser Cutting
Can be used to accurately cut thin sheet materials. - Other technology
Including bonding, mechanical fastening and thermal welding.
Surface Finishing
- As-Machining
Acetal’s CNC machined parts are machined to an excellent surface finish, and with the right cutting tools and parameters, a Ra3.2 finish can be achieved directly. - Spray Painting
Acetal spray painting requires a number of surface treatments to improve the adhesion of the coating for different colors. - Mechanical Grinding
Sanding removes the gloss from the surface, making the surface more suitable for painting or other coating treatments.
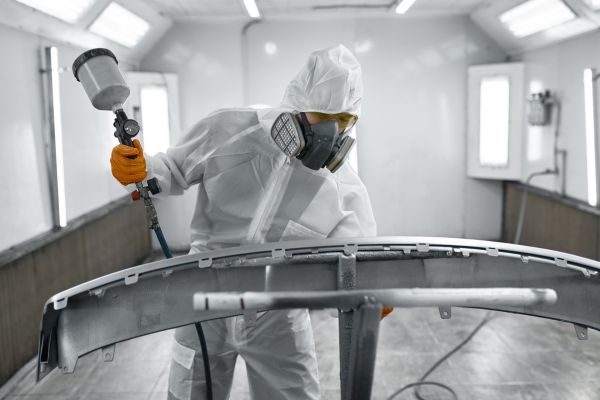
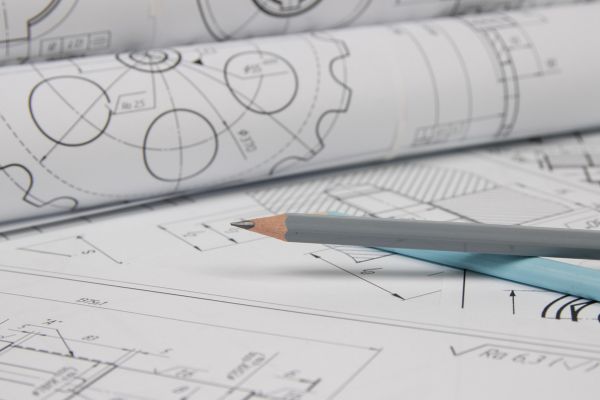
Design Recommendations
- Designed to the Standard Dimensions of the Material
Acetal is normally supplied in standard thicknesses in sheet or solid bar. Standard sizes should be used in design wherever possible to minimize material waste and processing costs. - Avoid Pursuing Minimum Wall Thicknesses
Minimum wall thickness designs may be difficult to fix and reproduce and may result in material bending, distortion or vibration. Best practices in machined designs should be used to improve reliability and economy of production. - Simplified Design
Complex designs often mean higher machining costs. Simplifying the design of a part and minimizing unnecessarily complex features can significantly reduce the cost of machining time.
Technical Parameters of Acetal
- Delrin®150
- Delrin®100 (AF)
Property Name | Numerical Range |
Tensile Strength, Yield Strength (MPa) | 73-76 |
Elongation at break (%) | 25-45 |
Hardness (Rockwell M) | 94 |
Heat Deflection Temperature at 0.46 MPa (°C) | 160-169 |
Melting point (°C) | 175-178 |
Property Name | Numerical Range |
Tensile Strength, Yield Strength (MPa) | 53-56 |
Elongation at break (%) | 10-19 |
Hardness (Rockwell M) | 77 |
Heat Deflection Temperature at 0.46 MPa (°C) | 160-169 |
Melting point (°C) | 175-178 |