
Features Of Aluminum Anodized Parts
Aluminum anodizing is to form a protective film on the surface of aluminum parts or aluminum materials. Its function can prolong the service life and maintain the beauty of the surface of aluminum parts. In addition to this, there are many more advantages:
- Strong anti-rust ability
- Strong abrasion resistance
- Rich surface colors, more appearance choices
- Good flatness
- Reduce the cost of finishing
- Weight update, reduce shipping cost
- Reduce environmental pollution
- Wide range of applications

Aluminum Anodized Processes
Aluminum anodization is a surface treatment process, which uses metal or aluminum alloy as the anode, and uses the principle of electrolysis to form an oxide film on the surface of aluminum metal.Aluminum anodization can be done in various colors, controlled by positive and negative voltages and toners.The thickness of the anodized film is usually between 5㎛~25㎛.
Aluminum anodizing can have two different appearances:
- Natural anodized aluminum colors: The surface is the primary color of aluminum Aluminum alloy materials suitable for Natural anodized aluminum include 1XXX aluminum, 5XXX aluminum, and 6XXX aluminum.
- Aluminum anodizing colors: the surface is various colors, such as aluminum black anodizing, aluminum red anodizing.
Difference Between Aluminum Hard Anodizing and Aluminum Anodizing
The film of aluminum anodized hard anodized and aluminum anodized is different, and the processing technology and method are the same.
- The thickness of aluminum anodized film is between 5-25㎛.
- The thickness of the hard anodized film is 25-150㎛, the film thickness of most aluminum hard anodized is 50-80㎛, and the special product parts will be 125㎛.
- The surface of aluminum anodization is smoother, and the surface of aluminum hard anodization is rough, and the thicker the film thickness, the rougher the surface of the CNC machining parts.

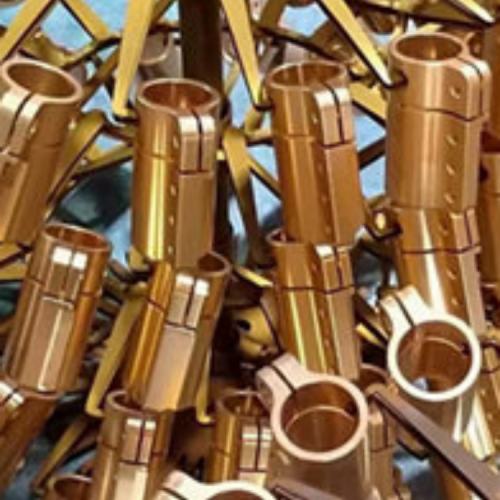
Applications of Anodized Aluminum Parts
Anodized parts are widely used, choose the right type of anodization according to your industry. The Tirapid team has rich manufacturing experience to provide you ,with more reasonable aluminum anodizing services.Aluminum anodizing is suitable for the following industries:
- Racing and custom motorcycles
- Consumer Electronics
- Robot
- Automation equipment
- Medical equipment
- Marine equipment
- Lab equipment and supplies
- Testing equipment
- Rapid prototyping
- Types Of Aluminum Anodizing
- How To Tell If Aluminumis Anodized
Aluminum anodizing is the most common surface treatment process in CNC machining. More than 90% of the parts manufactured by Tirapid need to be anodized.Different materials, tight tolerances, and choosing the right anodizing are critical.
Aluminum Anodizing
The thickness of aluminum anodized film is generally 3-10㎛, which is often used for products with surface anti-corrosion and aesthetic requirements. For example, consumer electronics, aluminum alloy doors and windows, etc.The aluminum anodized surface is flat and smooth.
Aluminum Hard Anodizing
Hard anodizing thickness is generally more than 15㎛. Hard anodizing is often used for parts with stricter functional requirements, and is more suitable for wear-resistant and electric-resistant occasions, such as auto parts, anodizing aluminum motorcycle parts, etc.
Aluminum hard anodized surface is rough.Aluminum hard anodizing is often used for aluminum materials 2017 aluminum, 5052 aluminum, 7075 aluminum.
Aluminum Anodizing Colors
When your aluminum parts need to be done in a variety of colors, the first thing to consider is aluminum anodizing. It can form a layer of film with various colors on the surface of aluminum parts, most of which are used for appearance products, which are beautiful and anti-corrosion.Aluminum is cheaper than stainless steel, and no matter which processing method is used, the processing cost is also the best choice.Therefore, in CNC machining, aluminum alloy anodizing color is the most commonly used surface treatment process.
Cast Aluminum Anodizing
The composition of die-cast aluminum will affect the effect of anodizing, and there are often irregular pores or impurities on the surface. If natural anodizing is a very challenging one, black aluminum anodizing without too strict requirements on the surface is totally fine.Anodizing a380 aluminum is the most common type of die-cast aluminum anodizing.
Aluminum anodic oxidation is the most common kind of metal surface amount, in addition to aluminum, there are titanium, magnesium and other metals are also suitable for anodic oxidation.
Sure.The outer dimension of the aluminum hard anodized parts will become larger, and the inner hole size will become smaller. For example, the inner hole of the aluminum part is 10mm, and after the aluminum hard anodized, the inner hole size will be reduced by 0.02mm.
The material composition of the parts, the oxidation solution type, the oxidation time control, and the ambient temperature of the operation can all determine the anodized color of aluminum.
The composition of aluminum material is an important factor in determining the color of anodizing.Die-casting aluminum alloys, non-standard aluminum alloys, 1XXX aluminum(1050,1060) and 7XXX aluminum(7075) materials are not suitable for aluminum hard anodizing colors.
Tirapid offers a comprehensive aluminum anodizing process, and according to your part needs, our mechanical engineers can recommend the most suitable anodizing for you. Save more processing costs for you and meet your needs.
If you want to know more in more detail, please contact Tirapid’s team of experts.