Nylon is a synthetic polymer that belongs to the group of polyamides (Polyamide, PA) and consists of repeating amide links (-CONH-). It was originally developed by scientists at DuPont in the United States in 1935. Nylon is strong, abrasion resistant, lightweight and corrosion resistant.
Through a variety of processing technologies, we can produce complex nylon parts quickly and accurately to meet the needs of diverse markets such as automotive, aerospace, and medical devices.
Types of Nylon
Each type of nylon can be modified by adding additives such as glass fibers, flame retardants, impact modifiers, and other additives to enhance certain properties needed for specific applications.
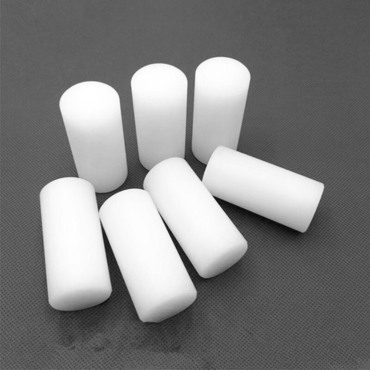
Nylon 6 is made from the polymerization of caprolactam. It has excellent mechanical properties and wear resistance. It is suitable for making plastic fasteners, gears and bearings.
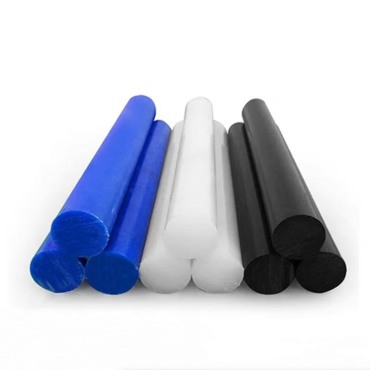
Produced by polycondensation of adipic acid and adipic diamine. Known for its high melting point and excellent mechanical properties .It is commonly used in automotive and automatization.
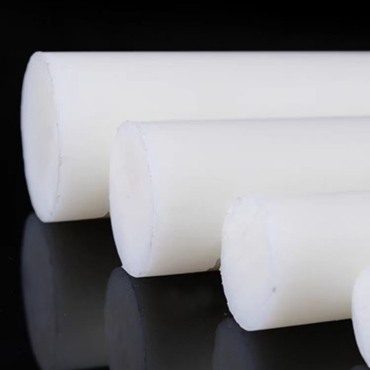
It absorbs less water than nylon 6 and nylon 66, which helps stabilize performance in wet conditions. Suitable for applications requiring dimensional stability and low water absorption.
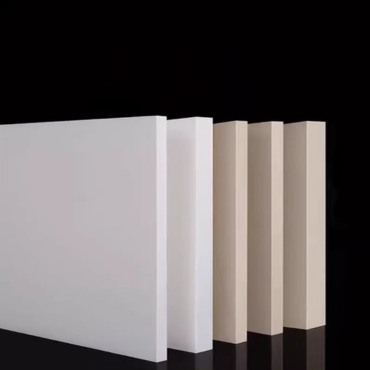
Derived from castor oil, it is a bio-based polymer. It has high flexibility, impact and abrasion resistance. Often used in the manufacture of pipes and hoses.
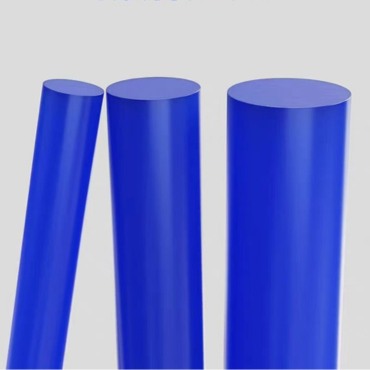
Similar to Nylon 11, but with lower water absorption for applications requiring superior chemical stability, such as coatings and the oil and gas industry.
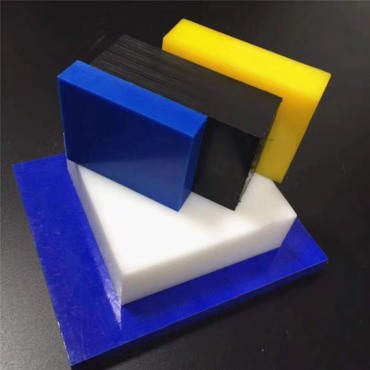
Has a higher melting point than Nylon 6 and Nylon 66 to maintain performance at higher temperatures for high-temperature applications.
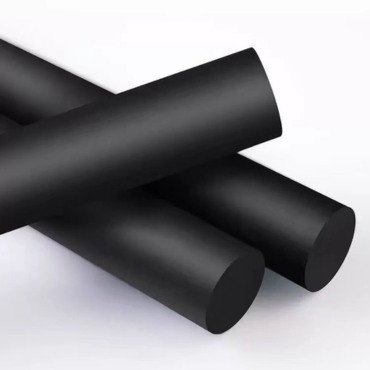
Nylon 6/6-6 is produced through a specific polymerization reaction and its main component is the copolymer of nylon 6 and nylon 66. It is widely used in various industrial fields and consumer.
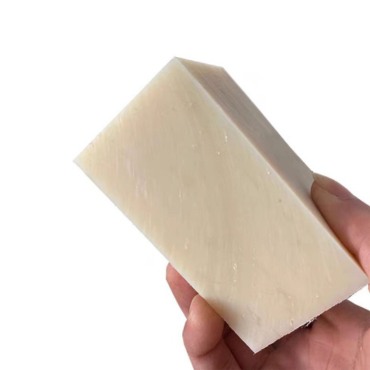
With lower water absorption than other nylons, it is commonly used in critical applications that require lower water absorption, such as electronic and electrical components.
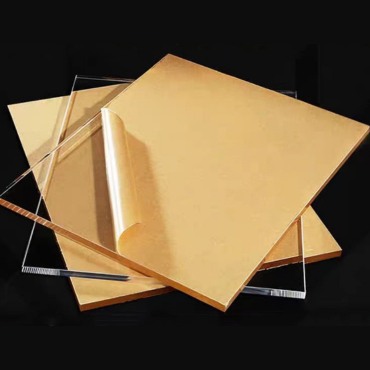
Nylon TR (often referred to as clear nylon or nylon TR-90) is a high performance thermoplastic material based on polyamide (nylon). It is commonly used in the eyeglass industry.
Nylon Material Advantage
- Excellent Mechanical Properties
Nylon exhibits excellent tensile and impact strength, can cope with significant mechanical loads and impact forces, and is very suitable for producing parts with high load-bearing capacity. - Good High Temperature Resistance
Nylon has a melting point of up to 255°C and exhibits excellent heat resistance. In high temperature environments, nylon can maintain the stability of its mechanical properties. - High Rigidity and Hardness
Nylon has high rigidity and hardness, providing strong structural support and wear-resistant surfaces, suitable for manufacturing precise mechanical parts. - Outstanding Chemical Stability
Nylon performs well in resisting grease, fuel, solvents and other chemicals, and is widely used in the chemical, automotive and electronics industries.
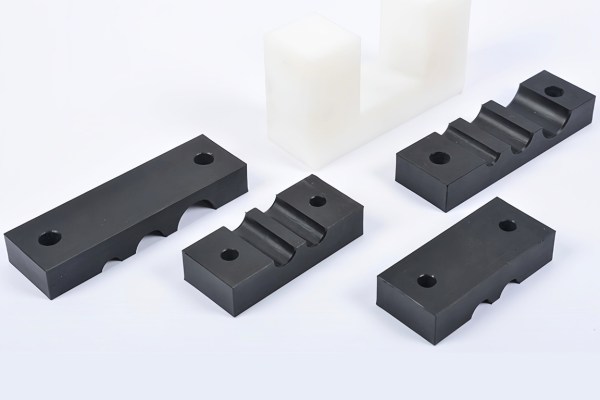
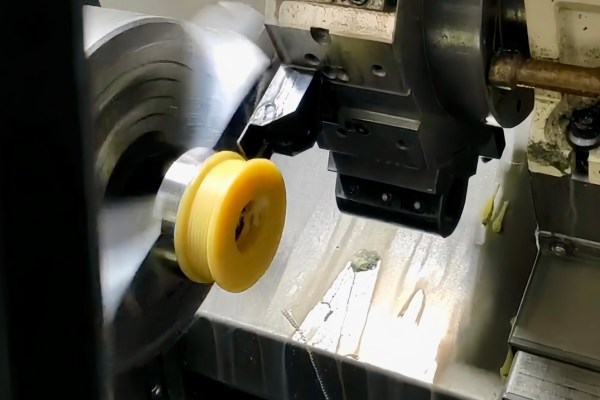
Nylon Machining Technology
- CNC Turning
Precision machining of nylon using high speed steel or carbide tools ensures the accuracy and surface quality of the part. - CNC Milling
Controlling cutting speed and feed rate is critical to avoid overheating the material. Proper cooling and specialized cutting tools are key. - Drilling & Cutting
Drill holes using sharp drill bits and proper cooling techniques. Laser cutting or waterjet cutting can reduce physical contact.
Nylon Surface Finishing
- Deburring
Removes tiny spikes or burrs created during the machining of nylon parts. This is accomplished by mechanical sanding, grinding wheels, or ultrasonic cleaning to ensure smoothness of the part. - Painting
By spraying a coating onto the surface of the nylon, you can improve its appearance, add color, and provide an additional layer of protection such as UV protection and scratch resistance. - Electroplating
Utilizing electrolysis to form a metallic coating on the surface of nylon enhances the abrasion and corrosion resistance of nylon parts while providing a smooth metallic appearance. - Hardening Process
Enhancing the hardness of nylon surfaces by chemical or heat treatments improves their resistance to scratching and abrasion. Hardening extends the life of the part.
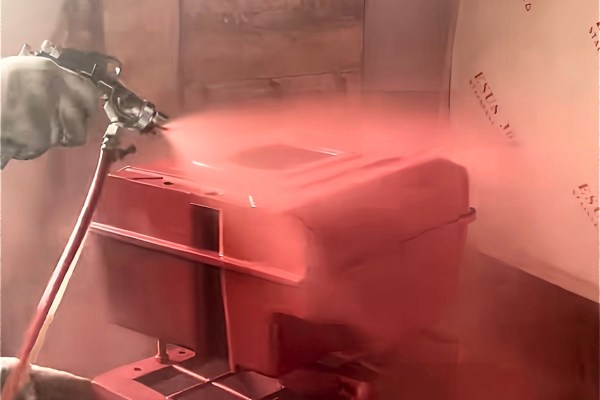
Nylon Material Performance Parameters
Characteristic | Numerical Value |
Intensity | 1.14 |
Melting Point | 260°C |
Hardness | 70-80 |
Water Absorption | 2.5% |
Heat Distortion Temperature | 70°C |
Tensile Strength | 50-95MPa |
Yield Strength | 45-85MPa |
Elongation | 60% |