Custom Online CNC
Machining Services
We offer fast and precise CNC machining services, tailored for the efficient production of metal and plastic prototypes and components.
Get an instant online quote and enjoy competitive prices for custom machining.



- Free Design
- No MOQ Required
- 5 Axis Machining for Complex Parts
- Large Part Machining (up to 118″)
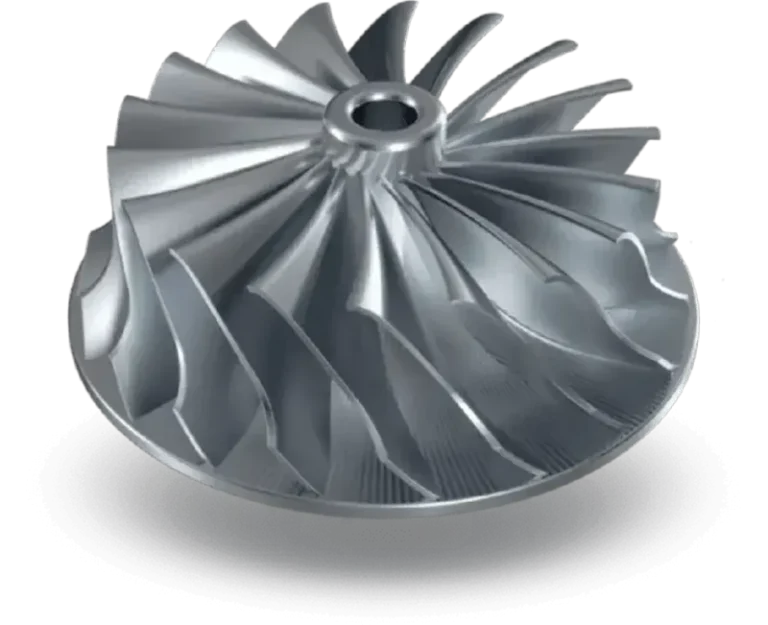
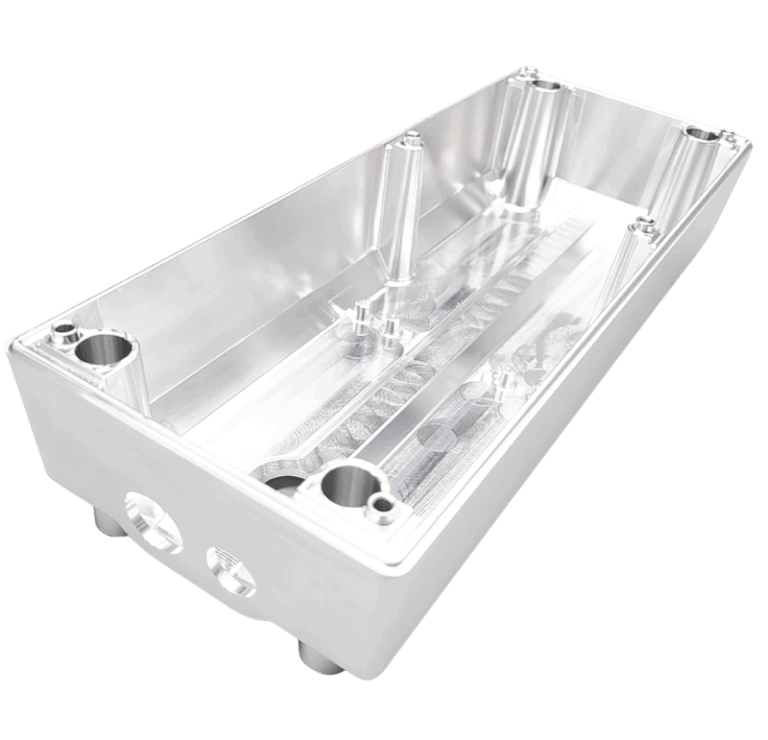
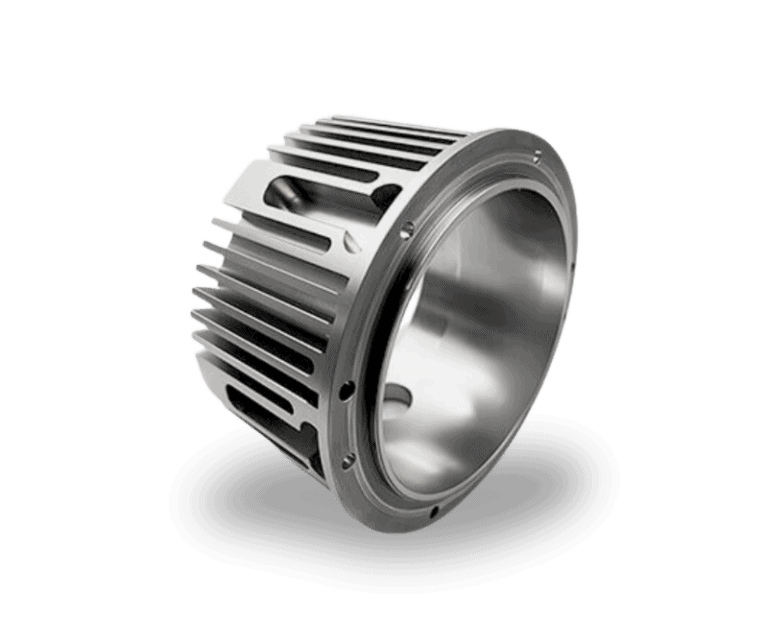
Our Manufacturing Capabilities
From prototyping to full-scale production, we provide customized solutions with ISO 9001:2015-certified
quality control—ensuring every component meets the highest standards of accuracy and reliability.
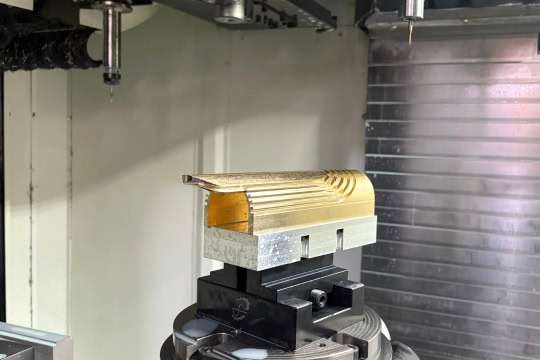
3 & 5 Axis CNC Milling
5-axis machining can precisely process complex surfaces, multi-faceted and angled features, reducing machining time.
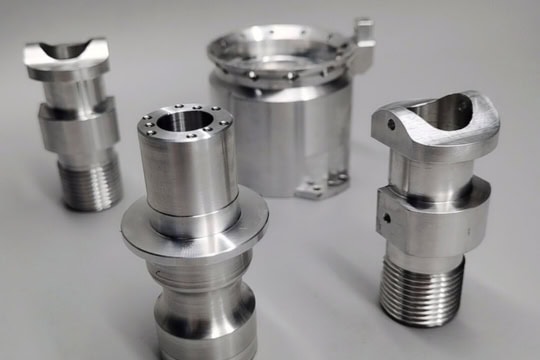
CNC Turning
CNC turning can accurately produce circular and cylindrical parts, providing high-quality surface finishes.
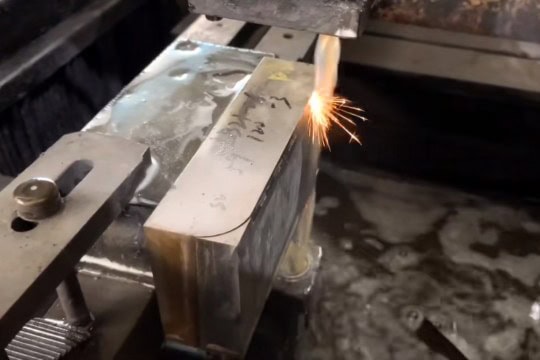
EDM
EDM can machine high-hardness materials, sharp corners, right angles, and complex contours.
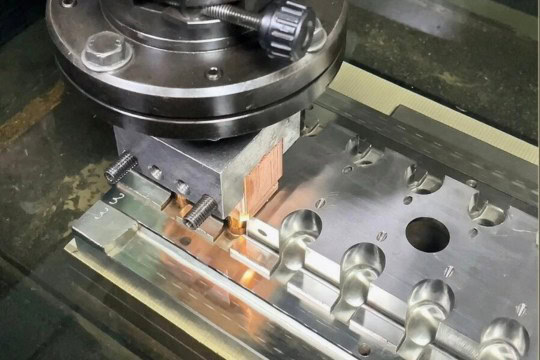
Wire EDM
Wire EDM is capable of cutting deep holes and producing high-precision, fine contours in parts.
Materials We Work With
CNC machining is suitable for processing a variety of materials, can stably achieve high-quality production, and is suitable for batch processing of different materials such as metals, plastics, and composite materials. We have more than 40+ kinds of materials that can be processed, the following is just a small list of materials.
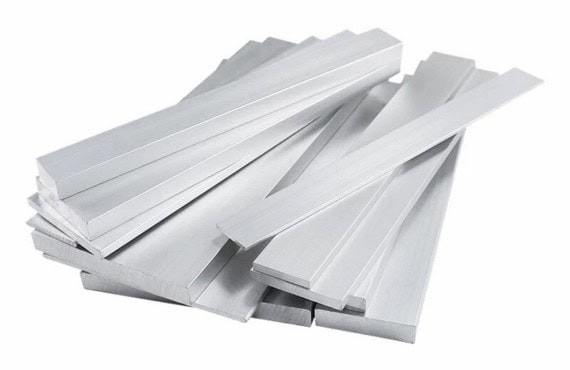
Metals
- Aluminum 6061/7075/6082
- Stainless Steel 304/316
- Steel 1018/4140/A3/A2
- Brass C36000/C28000
- Copper C11000
- Titanium Grade5/Grade1
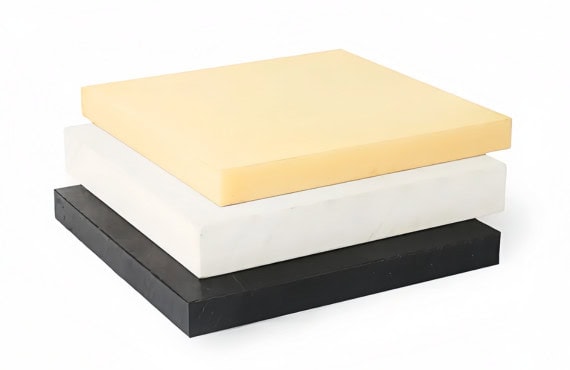
Plastics
- POM
- PEEK
- PVC
- PTFE / ABS
- ABS / PC
- PP / PEI (ULTEM 1000)
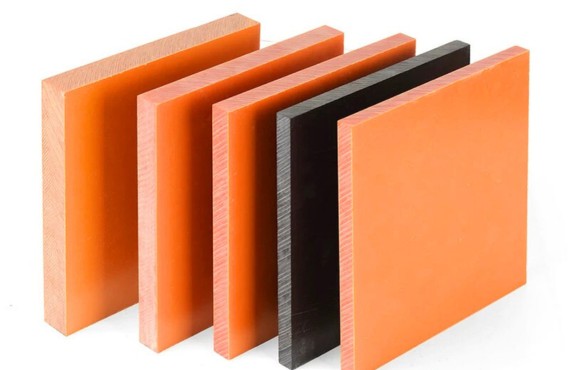
Composites
- CFRP
- AFRP
- BFRP
- MMC
- PMC
- GFRP
Why Choose TiRapid
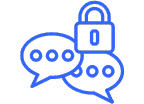
Secure & Confidential Manufacturing
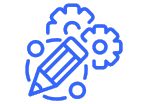
Full-Spectrum Manufacturing Capabilities
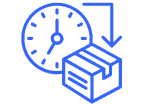
Fast Turnaround & On-Time Delivery
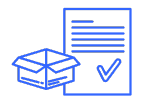
No Minimum Order Quantity (MOQ)

Multi-Material Manufacturing Options
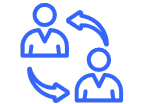
Design & Process Optimization
Our Project Team
We are a knowledgeable, lean and experienced team of engineers. To contact us,
please see the contact details below and one of our team members will be happy to assist you.

Bella Liang
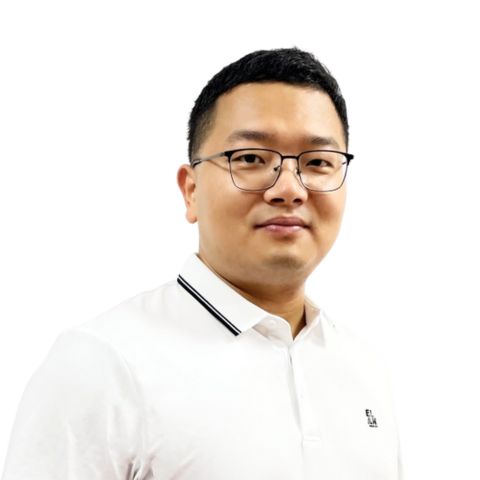
Galen Cui
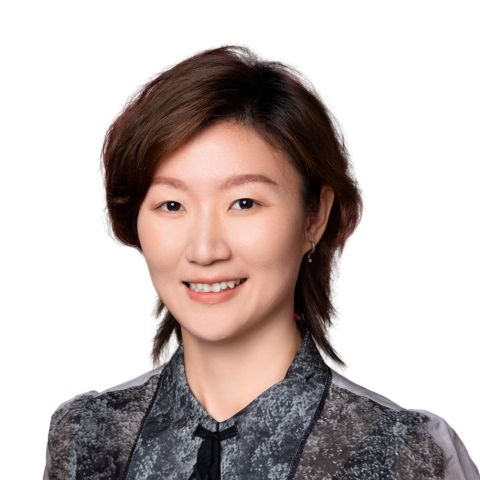
Maggie Du
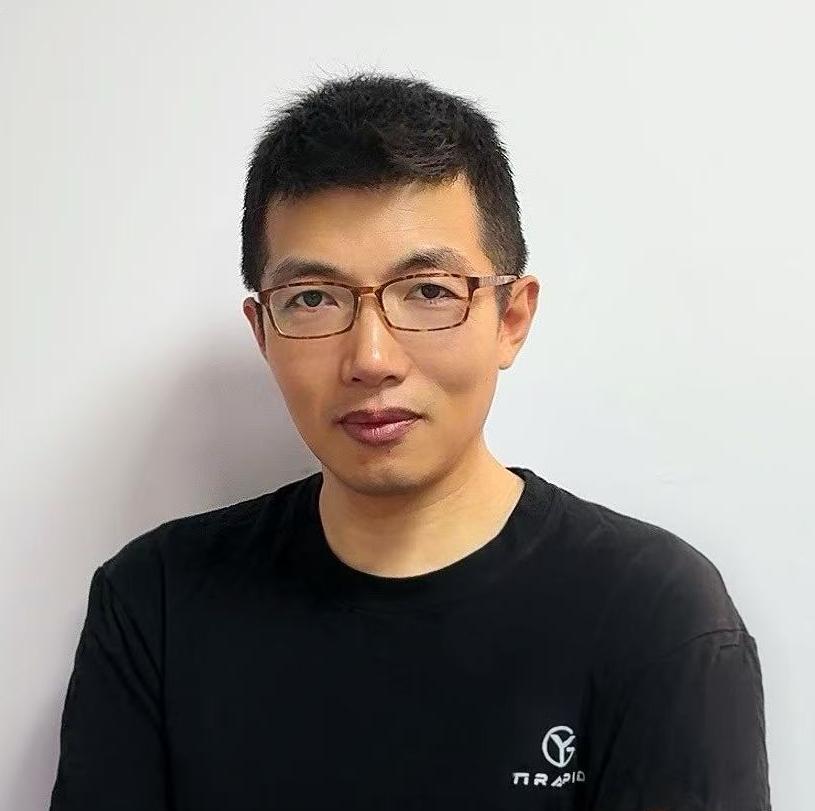
Nick Zhai
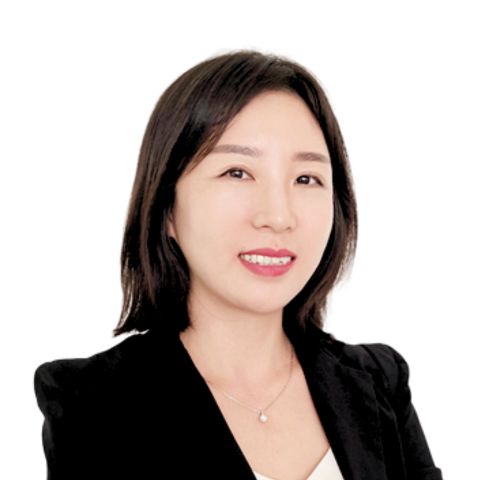
Rea Tang

Zoey Yong
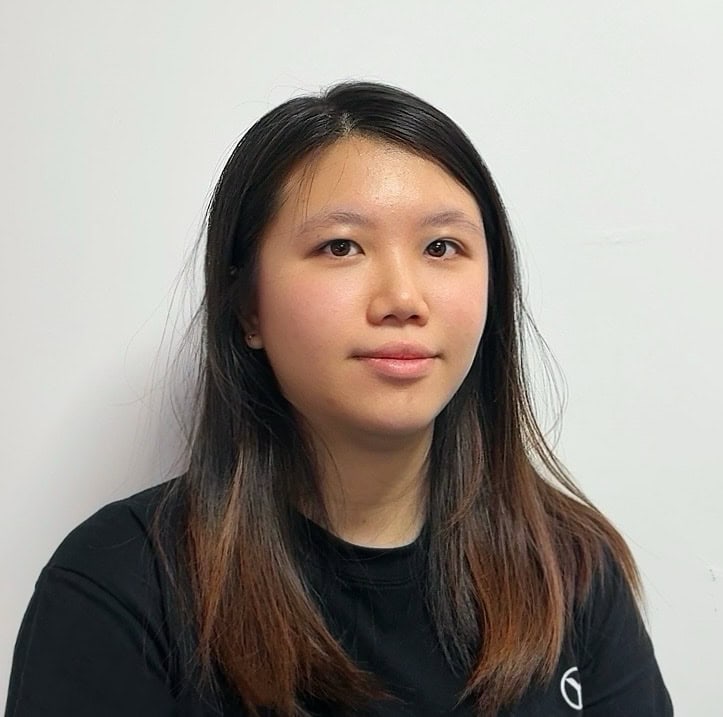
Kaya Chen

Lin Fu
Trusted by 3,00+ Companies for Manufacturer
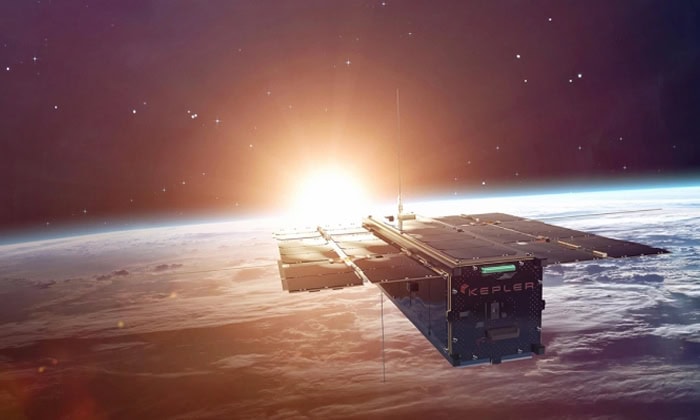
Aerospace & aviation
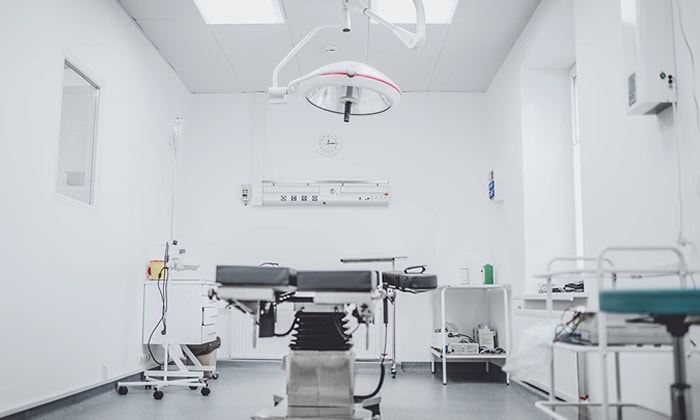
Medical Equipments
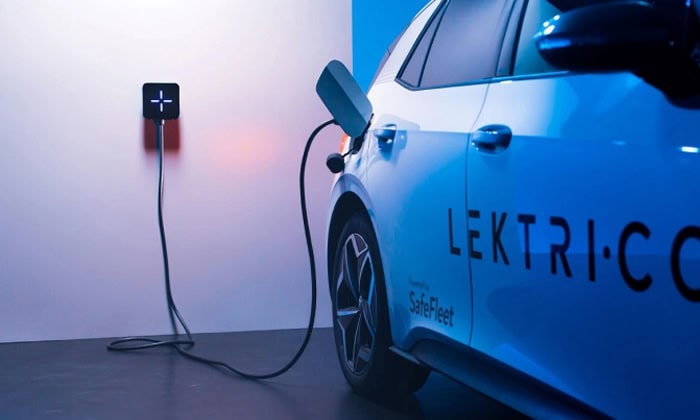
Aerospace & aviation
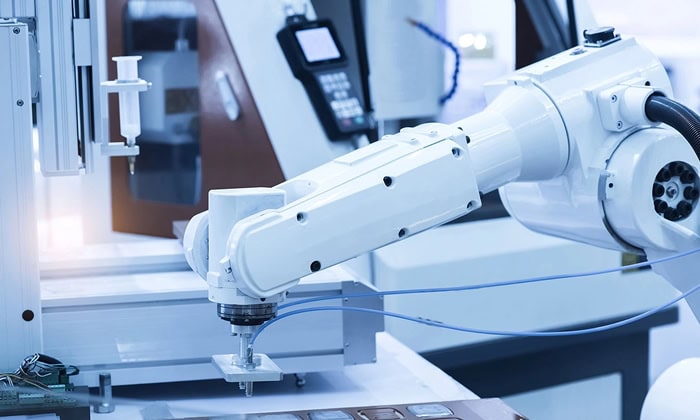
Robotics & Automations
TiRapid's track record





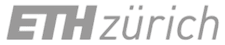



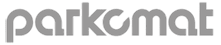
What Our Customers Say
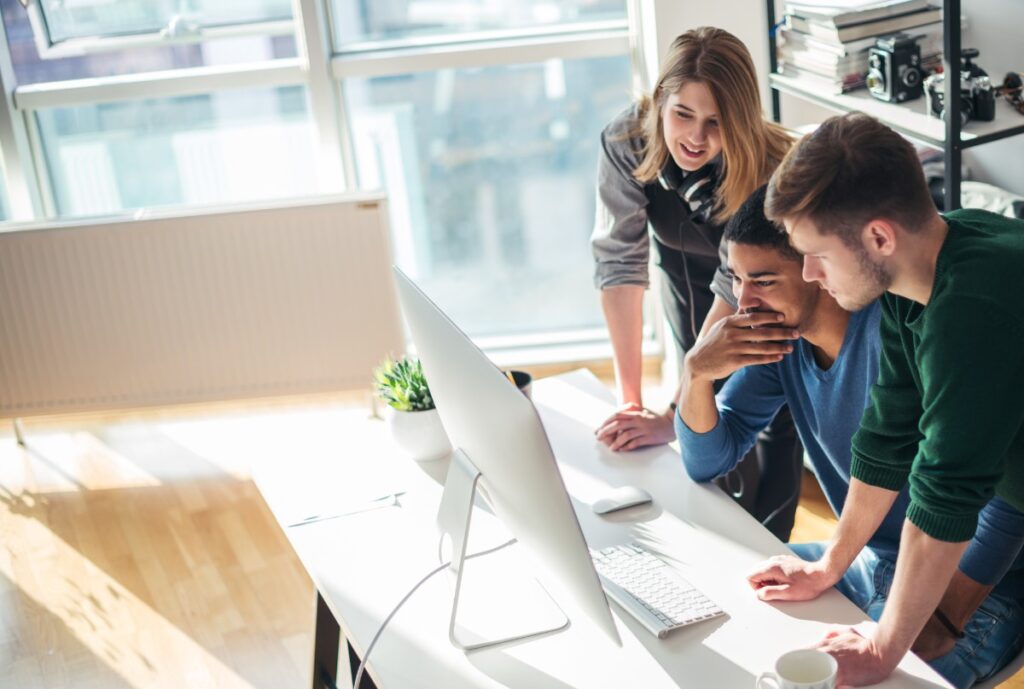




Frequently Asked Questions
Can you make my precision machining parts?
Absolutely! We specialize in high-precision machining, not only providing tolerance accuracy of ±0.01mm, but also completing other high-demand tolerances, such as form and position tolerances, surface roughness, surface curvature and other high-demand machining.
Does TIRAPID have the equipment to handle complex parts?
We have advanced processing equipment, including 5-axis CNC vertical machining centers and Swiss lathes, which enables us to efficiently process a variety of complex parts. Whether you need simple plane cutting or multi-faceted and multi-angle complex parts, we can easily handle it. Our technical team has 16 years of 5-axis machining experience.
What materials can TIRAPID machining?
We work with a wide range of materials, including aluminum (6061, 7075), stainless steel (304, 316), titanium alloys, copper, and engineering plastics like POM, ABS, and PC. If you have special material requirements, such as high-hardness alloys or custom materials, our procurement team can provide tailored solutions. All materials comply with international standards, such as RoHS and REACH.
How fast can you deliver parts?
TIRAPID is known for its quick response times. Standard orders are completed within 7-10 days, while urgent orders can be prioritized and delivered within 3-5 days. Our flexible production schedule ensures that you receive high-quality parts without delaying your project timeline. If you’re working on a tight deadline, feel free to contact our team, and we’ll provide the fastest delivery plan.
How does TIRAPID ensure product quality?
We follow a strict three-stage quality inspection process:
- Material Inspection: All raw materials are thoroughly checked before entering production to ensure they meet project requirements.
- In-Process Inspection: Operators and inspectors monitor every production step in real-time.
- Final Inspection: Before delivery, we perform comprehensive quality checks using advanced equipment, such as CMM and projectors, to ensure all parts meet your specifications.
Additionally, our quality management system is ISO 9001:2015 certified, providing you with complete peace of mind.
Can you handle small batch orders?
Of course! We have no minimum order quantity requirements. Whether you need a single prototype, 10 pieces for a small batch, or thousands for mass production, we can handle your needs with flexibility. For small batch orders, we also offer quick-turnaround services to help you validate designs and move your project forward faster.
What payment methods do you accept? Are they flexible?
We focus on fast response and efficient communication. Whether you contact us by email, phone or online chat, our customer service team will respond to your questions within 1 hour on weekdays. During the project, our engineers will communicate with you at any time to ensure that every step meets your expectations. If the plan needs to be modified or adjusted, we will cooperate flexibly to ensure that your project is completed smoothly.
How is TIRAPID’s customer service? Is communication convenient?
We work with a wide range of materials, including aluminum (6061, 7075), stainless steel (304, 316), titanium alloys, copper, and engineering plastics like POM, ABS, and PC. If you have special material requirements, such as high-hardness alloys or custom materials, our procurement team can provide tailored solutions. All materials comply with international standards, such as RoHS and REACH.
Does TIRAPID have relevant experience or case studies?
Yes, we have served multiple industries, including aerospace, automotive, medical devices, electronics, and industrial machinery, with over 16 years of machining experience. We have produced more than 400K parts for over 180 global clients. If needed, we can share relevant case studies or successful project references tailored to your industry to give you added confidence.
What support does TIRAPID provide if issues arise after delivery?
Our after-sales team is always available to provide technical support. If the parts you receive have issues, such as dimensional deviations or surface quality concerns, we will promptly verify and offer solutions, including free repairs or reprocessing. We also support further optimization and adjustments to parts, ensuring your satisfaction throughout the project lifecycle.