
Online CNC Machining Services From China
Quick custom metal and plastic parts | Precise quotes within 4 hours | Delivery in 1 day | Free global shipping | International prices include duties | Custom packaging for all prototypes.
- ● Free Design
- ● No MOQ Required
- ● Competitive, Flexible Pricing
- ● Implement ISO9001:2015 certification
Your 24/7 Quote Service
Our Manufacturing Capabilities

Rapid Custom CNC Milling Services
TiRapid offers custom CNC milling services, utilizing 3-axis milling, 4-axis milling, and 5-axis machining to produce high-precision metal and plastic parts. Our milling services are particularly ideal: Rapid prototyping.Efficient production parts.Precision rapid tooling.
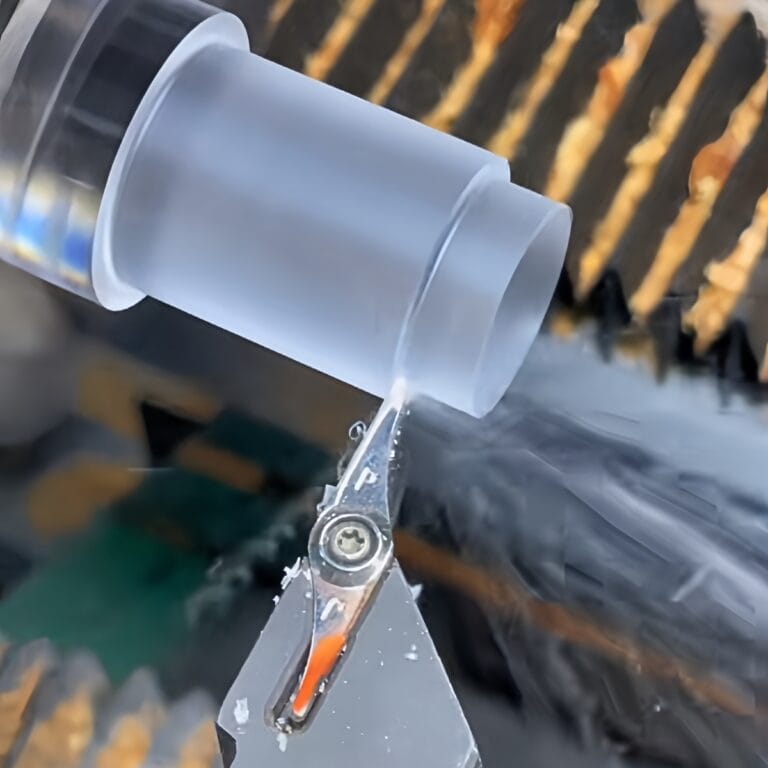
Precision CNC Turning Services
CNC turning is ideal for machining cylindrical parts. Our services use high-precision lathes and turning-milling composite machines, commonly used for shafts, bushings, and gears. Include: Rapid prototyping, High-precision batch production, Shaft turning parts with tight tolerances.
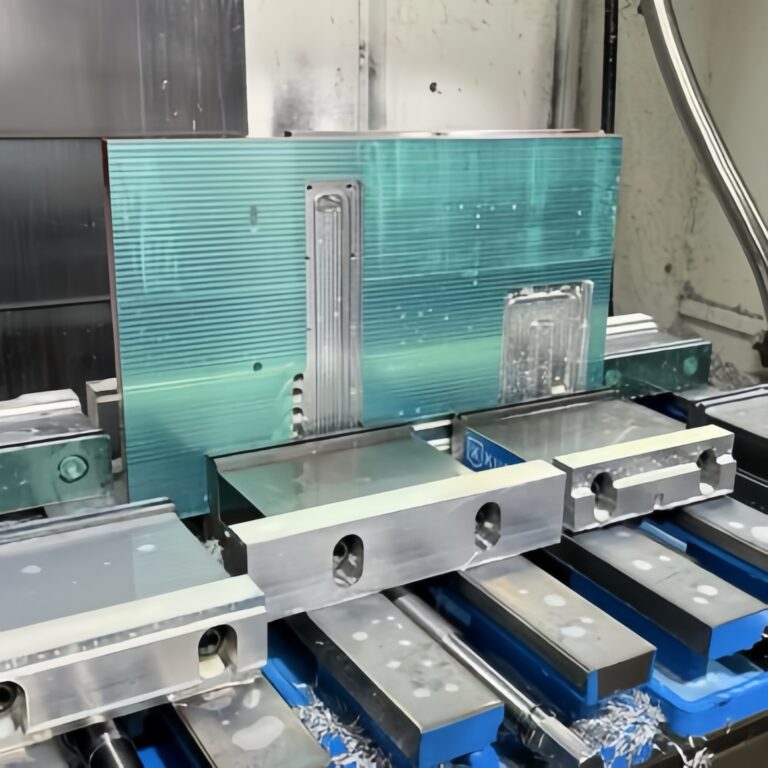
Large CNC Machining Service
TiRapid offers large parts machining up to 161“, with large-scale turning and milling capabilities. We achieve precision tolerances as tight as ±0.02mm, applied in medical equipment, automation systems, and aerospace components.
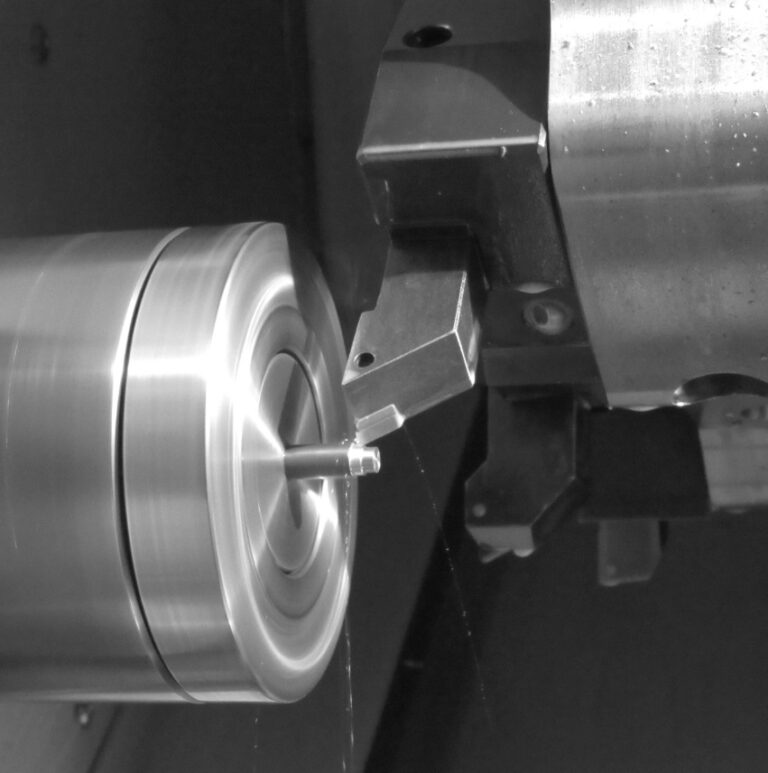
Micro CNC Machining Services
Micro CNC machining uses advanced mill and lathe technologies with multiple-axis motion to produce extremely small, precise parts. These highly specialized machines allow for the creation of intricate components with micron-level accuracy.
CNC Metal Machining Parts
CNC Plastic Machining Parts
About TiRapid
Founded in 2010 and located in Zhongshan, China (near Shenzhen), TiRapid is a professional CNC machining manufacturer. We are equipped with advanced machinery, including 3-axis, 4-axis, 5-axis milling machines, large milling and turning machines, CNC lathes, and Swiss precision lathes, capable of handling a wide range of complex machining needs.
Whether it’s for prototyping, low-volume production, or intricate part machining, our expert engineering team provides customized solutions tailored to your needs. We have successfully delivered hundreds of machined parts across various metals and plastics, ensuring precision and efficiency in every project.
We are committed to understanding your requirements and delivering reliable, high-quality service, ensuring that each project exceeds expectations. TiRapid has established long-term partnerships with leading companies worldwide, serving industries such as aerospace, medical, automotive, and robotics.
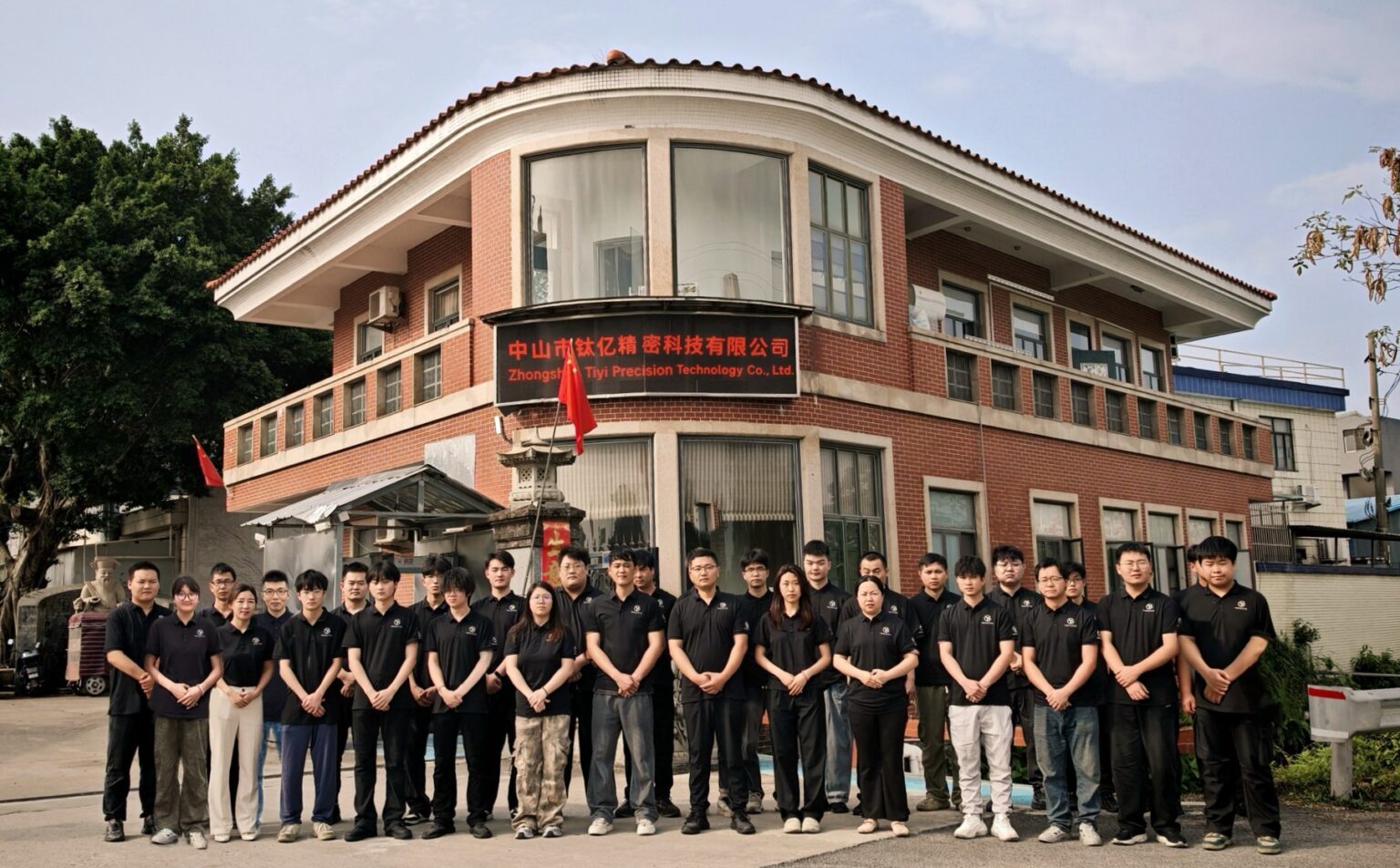
Why Choose Us
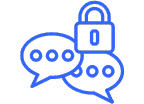
Secure and Confidential Manufacturing
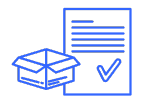
Reliable Manufacturing Capabilities
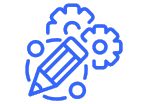
Accurate Quotes within 4 Hours
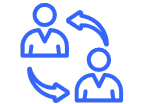
Manufactured and Supported in China
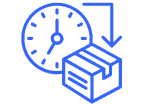
Fast Delivery
Our Certifications
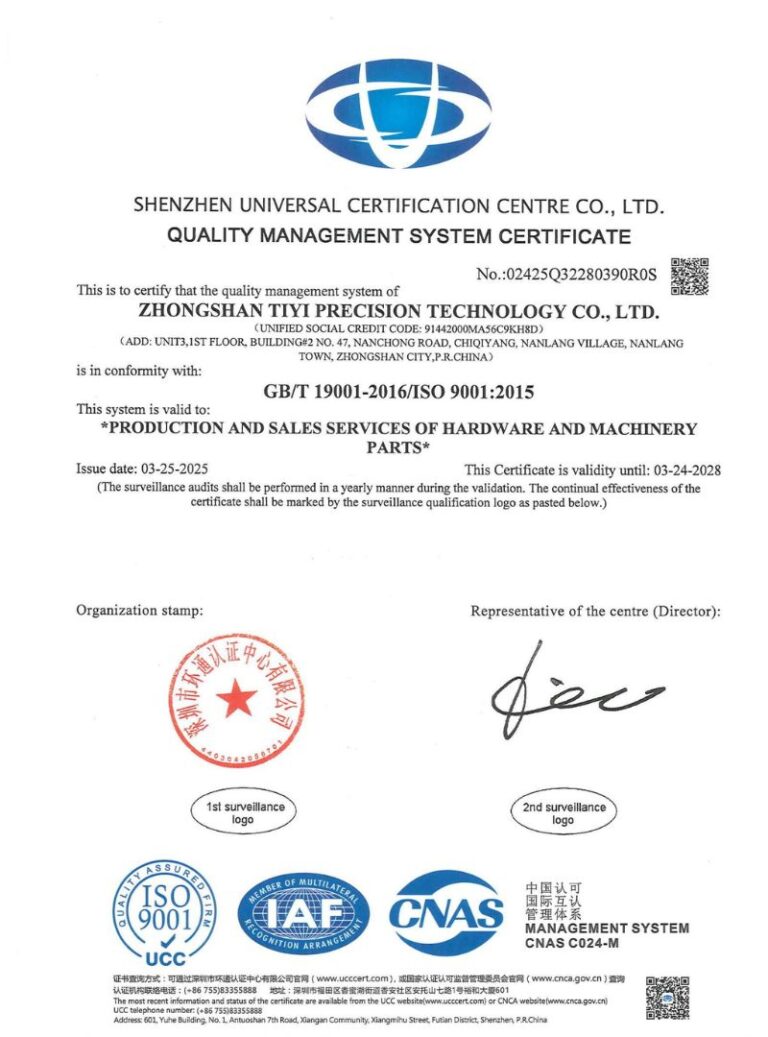

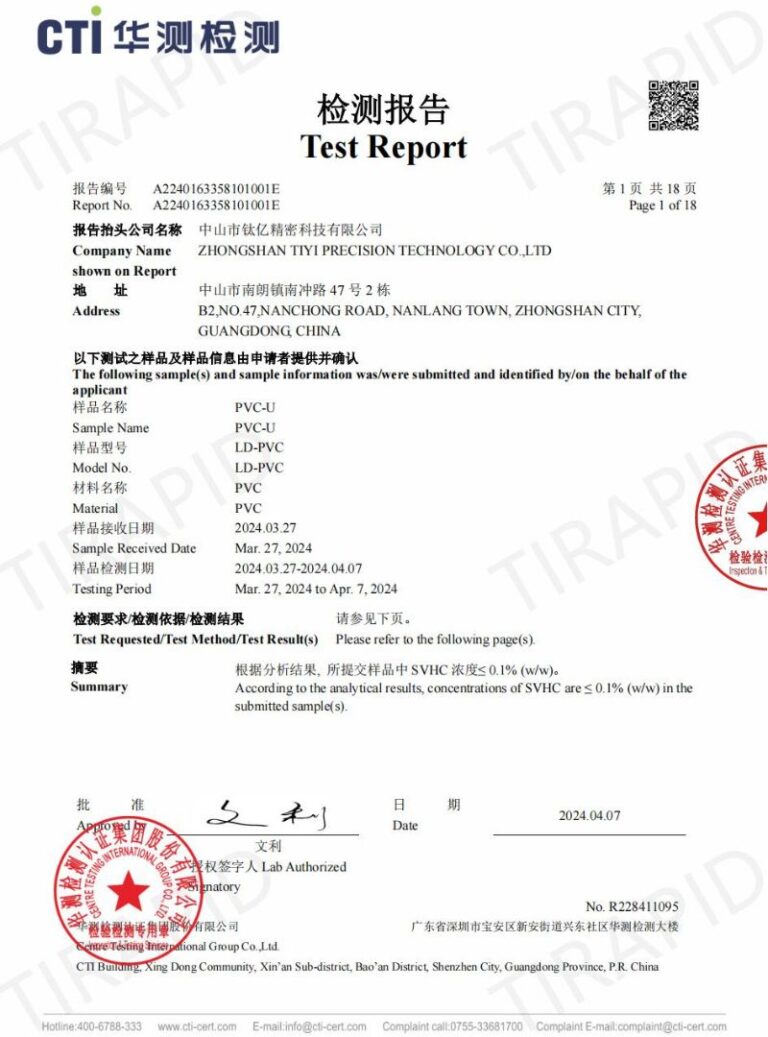
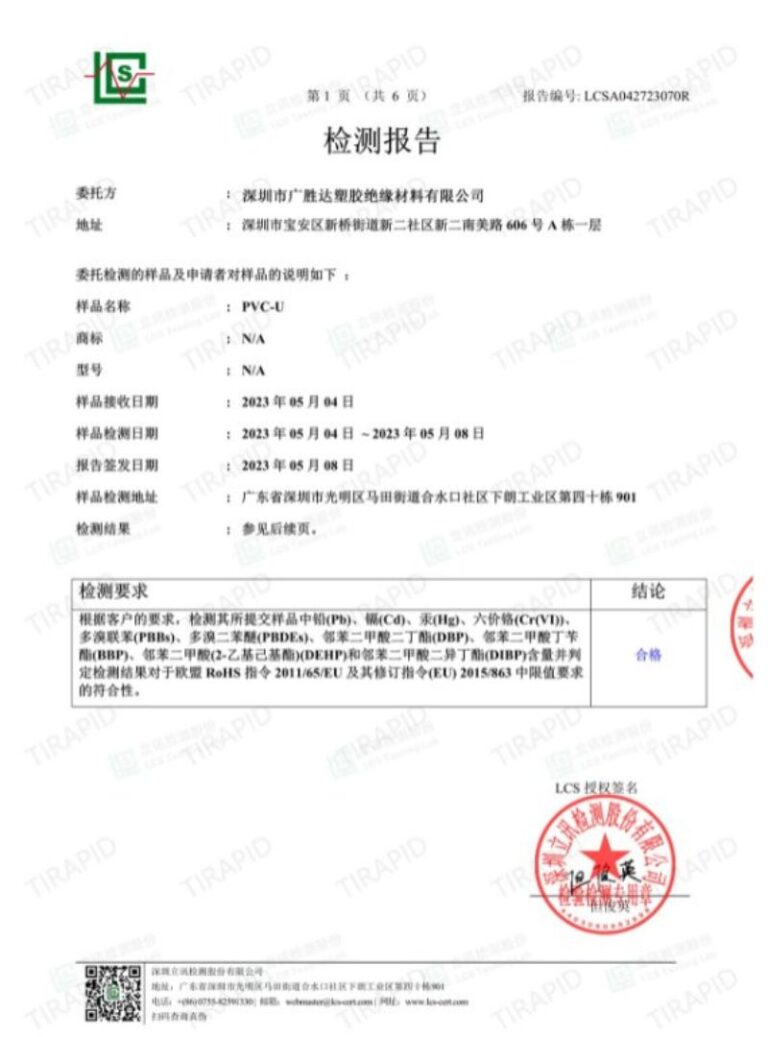
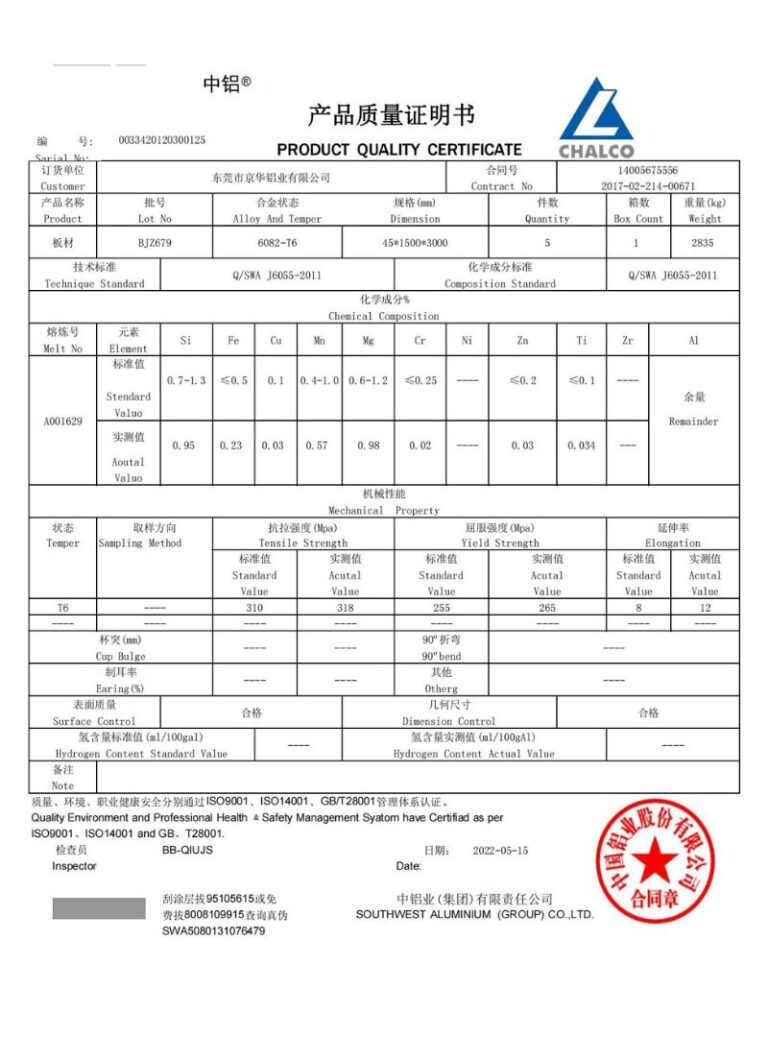
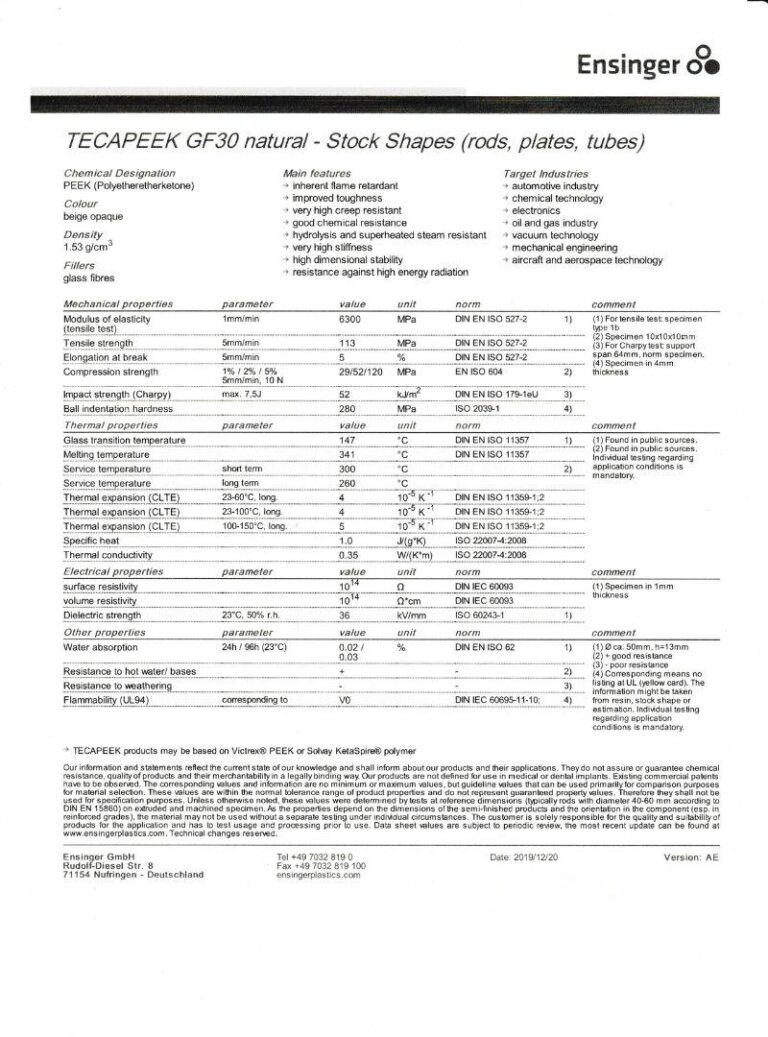
Frequently Asked Questions
How can I pay you as an individual? What are the payment terms?
It’s convenient for your payment. We have EURO and USD company account, and paypal personal account(+4% handling fee).
How fast can you deliver parts?
TIRAPID is known for its quick response times. Standard orders are completed within 7-10 days, while urgent orders can be prioritized and delivered within 3-5 days. Our flexible production schedule ensures that you receive high-quality parts without delaying your project timeline. If you’re working on a tight deadline, feel free to contact our team, and we’ll provide the fastest delivery plan.
How does TiRapid ensure product quality?
We follow a strict three-stage quality inspection process:
- Material Inspection: All raw materials are thoroughly checked before entering production to ensure they meet project requirements.
- In-Process Inspection: Operators and inspectors monitor every production step in real-time.
- Final Inspection: Before delivery, we perform comprehensive quality checks using advanced equipment, such as CMM and projectors, to ensure all parts meet your specifications.
Additionally, our quality management system is ISO 9001:2015 certified, providing you with complete peace of mind.
Can you handle small batch orders?
Of course! We have no minimum order quantity requirements. Whether you need a single prototype, 10 pieces for a small batch, or thousands for mass production, we can handle your needs with flexibility. For small batch orders, we also offer quick-turnaround services to help you validate designs and move your project forward faster.
What are your shipping services?
We rely on top-tier couriers such as UPS, FedEx, and DHL to ensure timely, safe, and reliable delivery of parts to our customers.
Do you have any certification?
Yes, our products can pass ISO9001, ROHS & REACH certification.